Time for another column.
I have been busy over the last few weeks writing my share of a new FS/FSAE book that will hopefully be published in time for FS UK in August. The book is being published by Racecar magazine in the UK and is being written by several experienced Judges and Tech Inspectors.
My section is on the Design documents and the Design event and Judging. Others are writing about their area of expertise. Many of the various authors will be familiar to those who have attended Formula Student Germany in the past as I have been privileged to have them in my team of Judges.
As a Design Judge, I am sometimes told “But they do that in F1” as a reason to justify some aspect of design in a FS car.
That leads me to ask two questions.
- Why do you think they do that? and
- Because they do it in F1, does that make it a good idea?
The first question is often very difficult to answer, especially in recent years when aerodynamics has overruled all other aspects of design.
An example of this would be the steeply angled drive-shafts on last year’s Williams. They were angled in order to lower the height of the transmission, therefore making room for more airflow to the rear wing. Does that make it a good design? Well, possibly, if you were trying to manage 200kph airflow across the wing. In any case, the car was very unsuccessful and the team have reverted to more normal driveshaft angles on their latest car, which, if we are to go by the performance in the 2012 Australian GP, is much better than last year.
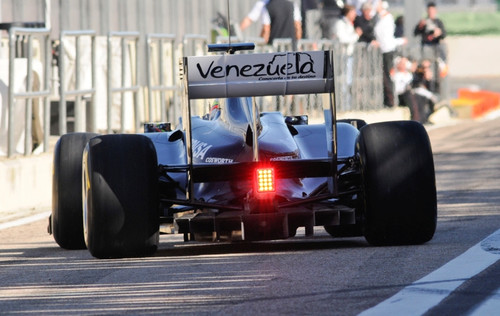
There is a power loss when a shaft is driven through an angle. The angular friction in the joint can be minimised by careful design as we were told by Williams last year. What cannot be ‘engineered’ out are the losses caused by the gyroscopic precession trying to straighten the shaft and the constraints made by the components at each end of the shaft. That loss might be minimal and justifiable when balanced against aerodynamic gain in F1, but, in a choked 600cc engine, we cannot afford these losses.
Teams will tell us the shaft maker says the shafts will operate safely up to 10 or 12°. That may be the case, but when driving power ‘around a corner’; there will always be a power loss. What the shaft maker is really saying is. “Try to run the shaft as straight as possible, but if suspension or steering operation turns these shafts through an angle, then keep it within the design limit”.
So, remember that when the judge looks askance at your angled drive-shafts.
Also at the Australian GP, I noticed the new Ferrari has reverted to pull-rods for the front suspension, the first time we have seen this solution for many years. The peculiar geometry in F1 which has the chassis pivots much higher than the front upright pivots and the position of the steering rack in the chassis meant the pull-rod is almost horizontal.
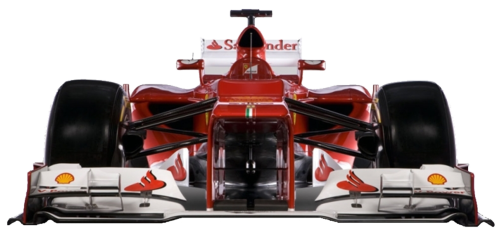
This puts an incredible compression load on the upper wishbone when the suspension operates. It will be interesting to see if Ferrari modifies this design, either by reverting to pushrods or lowering the rack in the chassis, before the season is finished.
When talking with student designers, most do not appreciate the horizontal loads that push-rods or pull-rods impose on the chassis. The upper link will be in compression with a pull-rod and the lower link will be in tension in a push-rod design.
In a push-rod car, this can easily contribute, with the braking loads, to pulling the inner clevis out of the chassis, especially in a composite chassis car, or breaking the inner rod ends if used.
Similar load cases exist in the pedal box, particularly on the brake pedal. The load applied to the pedal is multiplied by the pedal ratio when reacted by the pedal box. This load multiplication must be accounted for when designing the pedal box if a ‘flexy pedal’ is to be avoided. The pedal isn’t flexing, but the pedal pivot point may be. A similar situation exists with brake balance bars.
Sir Isaac Newton told us that “Every action has an equal and opposite reaction”. When designing any linkage, the engineer must be aware of where that reaction exists and how to feed it into the chassis with minimal compliance.
Whilst talking about the peculiar suspension geometry on current F1 cars, I was presented with an FS car a little while ago, with very similar geometry. The team did that because that made it ‘look like a Ferrari’. It didn’t, but in any case, the team scored no points for it. Why? Because I didn’t like it? No, they failed to score because they could not justify their decision! They did not know what the camber curves were or where the roll axis was. They made the decision, just because it looked cool.
Remember, Formula Student is an engineering design competition and the logic of the design decisions must be justified.
Pat’s Design Error of the month
This month I have two examples for your education or amusement.
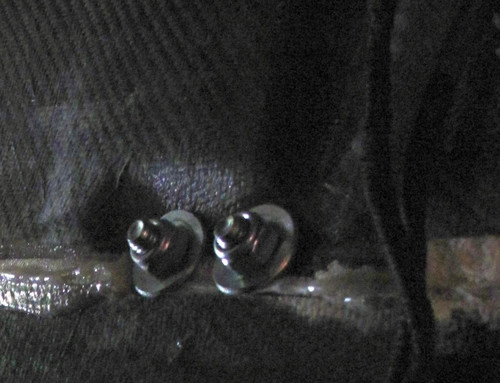
Firstly, I spoke about reacting the suspension forces into the chassis in the article above. This example shows a clevis fitting in a carbon tub. This car had pushrod suspension and the clevis shown is on the lower wishbone, so it is not hard to imagine what happens over a big bump when the pushrod force is reacted in tension in the bottom wishbone!
I titled this article ‘Understanding what you are trying to achieve’.
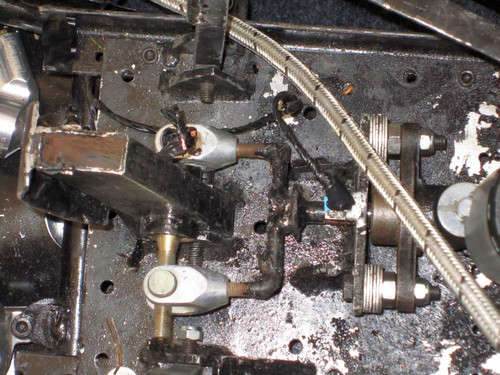
Clearly that was not the case with this design, one that I will post without comment.
Until next time
Regards