Apologies to all for the lack of a column over the last few months. Insane work pressure has kept me away from home for 7 of the last 9 weeks.
Last week had me in Adelaide where I witnessed the finish of the Solar Challenge. It was almost like being at a FS event as the front running universities all have active FS/FSAE teams.
Special congratulations to Tokai, who won the event over all and to Uni of NSW and Uni of Michigan at Ann Arbor who took the podium places. Incidentally, our friends from TU Delft have won the event on four occasions, in 2005 setting the record of 102.8kph for the 3000km crossing of the Australian continent. I am sure there is a huge store of electric vehicle information at Delft which will be shown to us in FSE!
When the Solar Challenge was started, the area of solar panels on each car was limited to 8m² based on the fact that each person on planet Earth has a potential space of 8m² of ground. The performance of cars like the Delft ‘Nuna’ forced the organizers to lower the area to 6m² and that may well be further reduced to 5m². Like FSE, the organizers are well aware of diminishing global resources and are doing something about it!
I like the idea that a car is like a Rubik’s cube puzzle, in that any adjustment causes changes in unexpected areas, just like setting up a car.
Car Setup, another variation on the Rubik’s cube.
Have you ever tried to solve a Rubik’s cube? You get one or two sides solved and then no matter what you do you mess up what you have achieved in trying to advance further.
Car setup is similar. Each time you improve one aspect of the handling, something else goes away. An example would be you have under-steer on turning into a corner so you do some adjustments to improve the turn in only to find you now have trouble putting the power down coming out of the corner!
Assuming the car is finished in time, the limited availability of track time and the cost of private practice means that most teams never get enough time to properly sort the car. Even worse, their drivers don’t get enough seat time to stabilize their personal performance so their ‘seat of the pants’ feedback is unreliable.
The availability of relatively cheap data loggers has not really helped because, in amateur hands, they tend to have the setup engineer (often the driver) micromanage the situation by concentrating on insignificantly small increments of too much data. How often do you hear a driver say something like “Toe it out half a millimeter and see what happens”. Michael Schumacher might feel a tiny adjustment like that but the average FSG driver will not and by attempting to do so will lose a track session. Some common sense logic needs to be applied.
First, it is important to know that the basic setup of the car contains no hidden flaws that will lead you astray. These settings need to be noted in a notebook and any changes recorded. You do keep a setup diary, don’t you?
- Check that tyre diameters are equal across the car (L R).
- Place scales (bathroom scales?) in position to go under the tire contact patch. With a straight edge and spirit level, shim until the scales are level across the car. Fore & aft is not so important. With the driver in position, use ramps to roll the car onto the scales.
- Disconnect the anti-roll bars (if fitted).
- Set the ride height and cross weight. If the car is heavier, front plus rear, on one side it is not possible to equal both the front an rear unless something can be relocated across the car, if not then the front is the most important to make close to equal because of its effect on braking.
You are now ready to set the suspension, KPI, Caster, Camber and Toe. Ensure the steering is locked in the central position.
If you have prior setup knowledge use it, if not check that the KPI and Castor are the same on both sides. It is not generally understood that both Caster and KPI will cause a change in camber as the wheels are steered.
High KPI settings can cause the outside front wheel to develop positive camber which destroys both grip and tyres.
Baseline settings for Camber and Toe are as follows
For cross ply tires.
Camber front, 1° to 2° negative, rear 0° to 1° negative.
Toe out front ½°.
Toe in rear ½°.
For radial tires.
Camber front 3° to 4° negative, rear 1° to 2° negative.
Toe out front ½°,
Toe in rear ½°.
Make sure settings are even side-to-side.
If the front toe is not set evenly on each side, the toe will automatically centre on the track as a result of the caster/KPI effect. This will put the steering wheel off-centre and will upset any ackermann angle side to side.
If the rear toe is not centered, this will cause the car to ‘dog track’ on the road and will also cause the steering to go off centre as the driver corrects. It is very worthwhile to make sure the front and rear toe is equally split.
A mistake often made by students is to measure toe at only one side of the wheel, usually the front at the front and the rear at the rear. If you do this you must remember to adjust the toe you are measuring to only half the desired figure. Remember, the other side of the tyre where you are not measuring is moving too!
Finally, connect the anti roll bars; adjusting the links so there is no preload.
Corner weights
If scales are not available the corner weight can be set on the track. Get the tyres up to temperature and hot pressure, drive down the straight in middle of the road so as to not be affected by the road crown. With the brake bias to the front, apply the brakes HARD!
The lighter wheel will smoke first. Adjust the corner weight and repeat until both wheels behave similarly and then wind the brake balance bar back to its normal setting.
To optimise the brake balance, wind it towards the rear until the car becomes tail happy under brakes and then adjust one turn to the front. For wet or low grip surfaces you need to adjust more to the front.
Dampers:
In recent years the evolution of dampers has improved the on track performance of most cars. It is well worth while understanding how dampers work and how they can contribute to vehicle setup and improved performance.
The average sprung mass of the vehicle is approximately three to four times more than the unsprung mass, so it follows that rebound damping is approximately three to four times higher than bump settings. This is shown in the damper dyno graph shown below.
Excess compression damping force the car will be harsh and slide. Excessive rebound damping will cause the car to pack down over bumps as the damper does not permit the spring to recover quickly
To help understand the effect of dampers I have drawn up the following table
Bump | Rebound | |
High Speed controls | Un-sprung mass | Sprung mass |
Low Speed controls | Traction and cornering grip. Less for better traction Too little reduces cornering grip | Car transient response |
General damper advice for varying track conditions
Bumps | Run soft spring and anti roll bars Raise ride height |
Smooth fast corners | Run high rebound- bumps would jack car down |
Wet | Reduces “G” force, less weight transfer Lost grip takes longer to recover, need lots of low speed bleed. High speed almost dry setting for bump and rebound. |
Testing: Program suggestions
Warm up the tyres.
When making set up adjustments it is desirable to keep the tyres at operating temperature. Keep the tyre temperatures (and therefore pressures) consistent, ideally at the optimum temperature for the tyre.
Brake Balance.
Dial excess brake to the front. With no close following traffic, driving down the crest of the road brake hard, dial rear brake in until the rear wheels give an indication of locking first and then a turn back to the front. If one front wheel smokes before the other increase the weight on that wheel by winding up the spring platform/pushrod, or winding down the other side or doing the diagonally opposite adjustment on the rear.
Circuits with less friction need more rear brake bias, this shows up particularly in the wet.
Car Balance.
Adjust the mechanical balance on slow corners first, pick a safe corner with plenty of run off and set using the anti roll bars, spring rate, tire pressures and camber. If the car has some aero adjustment now set the high-speed balance again selecting a suitable corner.
Even if the car feels OK make some adjustment to get a feel for it. Make fairly large adjustments, if you go to far it is easy to go back, if you creep on it, it is hard to feel the difference.
For maximum cornering power correct the car end that lacks grip.
Under-steer: | Adjust the front, usually go softer. |
Over-steer: | Adjust the rear softer. |
Since car balance is most important for cornering speed, if it cannot be achieved in the time available by adjusting one end of the car, then adjust the other end of the car in the opposite direction.
It is desirable to keep the rear anti-roll bar stiffness to a minimum; this gives more independent wheel movement improving traction out of corners and on bumpy surfaces.
Finally, to maximize testing time on track, it is best to make fairly large changes so the driver can quickly feel the difference. It is easier to make a judgment to get the best setting available in the time available. Maybe all the sides of the Rubik’s cube will not be aligned, but enough will be to allow a safe and productive event and to give a good starting point next time you go to the track.
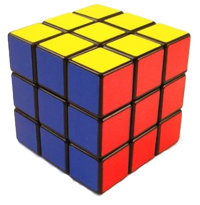
Oh, and you do keep a set-up diary, don’t you?
Cheers for this month
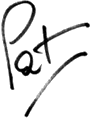
Pat
Pat’s Design Error of the Month.
What I am trying to show this month are errors made when the Designer didn’t fully understand the problems he was trying to solve.
Here, the axle design used a Universal joint, a Metalastic ‘donut’ and a sliding spline on the axle.
The splined joint is obviously there to accommodate axle plunge as the suspension articulates, however, unless the design is poor, the donut will accommodate any plunge.
The donut will also double as a flexible joint in the axle. The universal joint is a poor choice because when the axle moves, second order vibrations will be generated in the joint and will cause ‘whirl’ in the driveshaft/donut unless there is a locating pilot between the two donut flanges. I agree the donut will absorb driveline shock.
This is a heavy, ugly design that is liable to failure in operation. A far more suitable solution would have been to use a simple tripod joint as used on the inner end of the drive axles on almost every FWD car. The tripod would have permitted drive, articulation and plunge in one simple component.
The second design issue with this car relates to the way the wishbones have been made and mounted. Having the rod ends in line with the arms means they cannot be adjusted(for camber adjustment) without having to strain or even bend the wishbone arms when refitting them to the chassis.
The pull-rod and bell-crank are out of plane and it looks like the bell-crank pivot is on an unsupported tube where the torsional load is reacted. The upper end of the pull-rod picks up on a flat plate web on the upper wishbone. All these errors will result in compliance and geometrical issues in suspension operation.
In this example, the team has used their CNC ability to make an alloy rear upright. Rear toe is controlled by the bolt on bracket that connects to the toe control tie-rod.
Just looking at this I can almost make it flex! Rear toe stiffness is critical to making a car drivable, so designs like this must be avoided.
Until next time
Regards
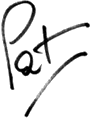
Pat