In a recent email exchange with my fellow Chief Design Judge Steve Fox, the subject of ‘compliance’ came up. Steve wrote the following comment and it prompted this latest Tech Column.
Compliance is something that…
- Their CADs can't predict.
- They don't think about because it is so simple. (They are always over-thinking things)
- Sneaks up on them because most of them do not have experience with accumulated tolerances (stack-up of accumulated tolerances).
- Is stupidly easy to check for (simple photo analysis, with reference lines drawn on the paper)
- Is difficult to detect with even a sophisticated DA system.
- Bites every competitor to some degree or another. (Some in a BIG way!)
At FSG in August, we asked at the Design Review Adventure “Where do the loads go”? The following discussion was about load paths and force dissipation into the chassis. This, of course, led to the inevitable discussion of compliance.
The question then asked was ‘How stiff does the chassis need to be’? When Dr Andy Deakin was at Leeds University sometime in the last century (sorry Andy) he authored an SAE paper on this very subject (2000-01-3554), a paper which should be required study for anyone reading this. I am not going to make it easy for you by including a synopsis here, read the original paper. While you are sourcing the paper, there are several more with a similar subject.
What happens so often is, a team attend the FSG competition and when asked about chassis stiffness, they quote a FEA figure to the judges. Without any verification this is pretty useless. The chassis structure may well reach the design stiffness goals, but in the real life, compliance in suspension mountings etc., means the total structure is far less stiff than the intended design.
Design Judges will ask about chassis stiffness or torsional rigidity and then about something called ‘installed stiffness’. The first is the calculated and/or measured stiffness of the structure alone. The second is the stiffness measured at the hub faces. This is always considerably less because of compliance in the suspension mounts and linkages, the hub carriers and hubs plus clearances in the wheel bearings and suspension spherical bearings. Incorrectly used rod ends will contribute to this compliance.
One factor not taken into account when measuring installed stiffness is the compliance in the road wheels! I have had a designer tell me categorically that it was impossible for his car to put a loaded wheel into positive camber, even when faced with photographic evidence. His design did not permit positive camber, however the compliance in the wheel assembly did.
Another area of loss of stiffness is what I call ‘clearance stacking’. This is particularly noticeable in steering and suspension mechanisms where a number of components requiring working clearance are used in series. These clearances all add together and the end result is lost motion, loss of accurate control of the mechanism and plain old ‘slop’. As the mechanism settles in with use, this slop gets worse.
A good example is a typical steering system. Teams are required to use a quick removal steering wheel hub. Even when new, there is clearance in this mechanism. The splined mechanisms are much better than the hexagonal units in this regard. There is then one (typical) or even two universal joints in the column, or with the advent of the foot-well template, a bevel gear set. These mechanisms have their own tolerances, which loosens up with use. Add to this clearance between the pinion and the rack, clearance between the rack and the housing and then clearances in the four rod ends used on the tie rids. All these clearances add up to significant lost motion even when the components are new. For this reason teams should invest in the best quality components they can afford.
The judges will always check for ‘compliance steer’ in the rear suspension of a car. Typically cars are set statically with about 3mm of rear toe-in, but compliance and clearance stacking in the components can often see toe variations of 20mm or more! This will result in a dynamic rear steer situation including a significant amount of toe-out. The result is a slow car that is very difficult to control.
Compliance and clearance stacking will also affect camber. This will go ‘positive’ under side loads to the detriment of grip and tyre life. Rear toe-out allied with positive camber makes for an uncontrollable car!
The usual cause of rear compliance steer is a lack of suitable toe base. Compliance and clearance stacking should be considered at the design stage. Usually, computer programs will not take into account clearances and structures are considered infinitely stiff or rigid. However, in the words of that wise old man, Sir Henry Royce (of Rolls Royce fame), “Everything is made of rubber”!
Structural compliance often sneaks into a tubular structure when different types or diameters of tube are joined. This can be seen in the illustrations. If such a join is necessary, the designer should look carefully at the geometry of the joint or use a doubler or stiffening web.
Bolted or riveted joints are a source of compliance if not engineered correctly. Repeatedly, the judges see structures, typically rear torque boxes, bolted together with allen cap screws screwed directly into aluminium and without a washer under the head. Apart from the small area under the head of an allen bolt, there is a radius between the shank and the head, part of the manufacturing process. These two issues cause the bolt head to work into the aluminium causing the structure to come loose and flex. An important part of design is the choice and utilisation of the correct fasteners.
On monocoque chassis, a common solution is to feed loads into a point on a flat panel. Invariably, this will ‘pant’ to some degree or another under load. I have written in a previous column about the importance of load paths. If the load is fed appropriately into a monocoque skin, then there should not be any serious problems. Yet we regularly see panels loaded perpendicularly. I feel this is not because the designer does not understand how to react the force, but because the designer can not visualise the vector of the forces.
I have mentioned compliance in suspension components and mounts causing unwanted variations in camber and toe. On tubular chassis, suspension mount clevises are often mounted to a sheet steel bracket welded to the chassis. This may be an easy way to mount suspension and permits easy shimming for camber adjustment, however, the chassis stiffness/compliance is reduced to that of the bracket.
We often see compliance in the upright assembly, and the load reversals from driving on a road course can lead to failures in the suspension components. Computer analysis may show the design to be adequate, but continual load reversals can lead to fatigue failure.
Hubs and wheel centres are often seen to be flexible. The cyclical flexing of a wheel centre can cause a fatigue failure and the loss of a wheel. I have first hand experience of this having been hit by an errant wheel an FSG 2009.
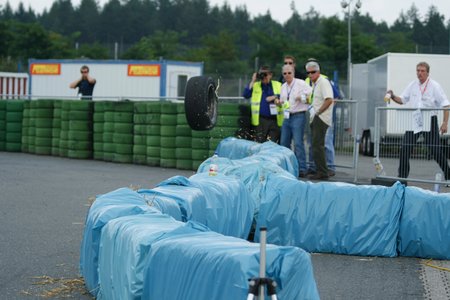
Inspection showed a classic fatigue failure caused by cyclical flexing of the wheel centre diaphragm. If observers report positive camber (particularly at the rear) yet the designer claims this cannot happen because of his knowledge of the suspension geometry, then suspect excessive compliance in the wheel, suspension components or the chassis suspension mounts. Truly, the camera doesn’t lie. Look critically at your still photographs for evidence of compliance!
So, how stiff does the chassis need to be? Well, I believe that ultimate stiffness in torsion and bending is not as important as some would have you believe. Compliance and clearance stacking is another matter entirely. More gains in handling and driveability are to be gained when those two demons are banished.
So, minimise clearances, spread the force reaction base and feed the loads into an appropriate node to dissipate the forces and your design will go from passible to impeccable without incurring the constraints in time, weight and resources that building an ‘uberstiff’ chassis entails.
Next month sees the tenth running of FSAE-Australasia at Werribee in Melbourne. There are 27 entries including two electric cars. Seven entries are from overseas teams but none this year from Europe. I guess the European calendar is so full that the Euro teams have neither the time nor the budget to come to Melbourne.
I will report on the event in my next column.
Pat’s Design Error of the month:
Obviously, this month’s error has to relate to compliance.
Stooging around at FSAE East in Michigan in May, I snapped the following pictures. I don’t think any commentary is necessary.
That’s enough compliance for this month!
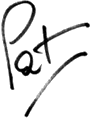
Pat